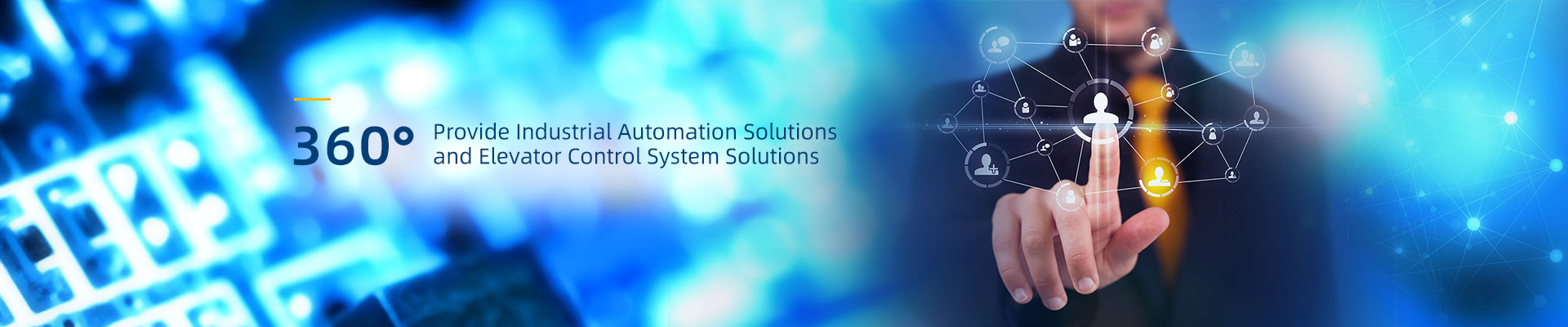
1 Foreword
With the development of processing technology for paper and plastic packaging and the updating of coating processing equipment, the tension detection and control of paper or plastic during the coating production process is an importantꦆ technical measure which can improve product quality and output.
The coating machine is a device that coats raw materials (paper, cloth, plastic, etc.) with an optional coati🧔ng (adhesive, ink, etc.), and then dries and winds up. In the whole process, it is divided into several processes of unwinding, intermediate multi-level synchronization control and winding. It is required that the paper tension is constant during the work, that is, the linear velocity is constant.
Technical requirements
1. Raw 💞materials must maintain constant tension during unwinding and rewinding
2. When unwinding and winding, regardless of the change in the roll diameter, a smooth and ౠconsistent line speed must be maintained.
3. Unwinding control, intermediate❀ multi-stage synchronous control, and winding control speed must be synchronized to avoid the raw materials being too loose or too tight, or even being pulled up.
2 Introduction of HD50
The modular and custom design of the HD50 series features excellent open-loop vector and closed-loop vector control for three-phase AC asynchronous motors and three-ph🐷ase AC synchronous motor control.
HD50 are high-pe♏rformance vector control AC drive which
The HD50 series has built-in extended function interface and multiple encoder interfaces, which can realize speed control, torque control, constant tension control and servo positioning control. It can meet the requirements of cran𒆙e machinery, printing machinery, high-end machine tool in many fields such as various kinds of complex high precision drive, and provide comprehensive solutions for the equipment manufacturing industry.
Features of HD50
1. Unique tension control function, multiple selection of tension control, built-in automatic calculation module of reel diameter, advanced inertia compensation algorithm, flexible taper adjustment,☂ and automatic detection for belt-broke𓄧n.
2. Various ⭕torque references, Flexible adjustment between the torque control and the speed control.
3. Higher perf💙ormance VC control, speed control accuracy: ±0.05%, speed control range: 1:1♎000, torque control response:<50ms, start torque: 180% rated torque /0Hz.
4. Due to the excellent current and voltage control algorithm and th🎐e advanced overcurrent suppression, the inverters will run without overcurrent and tripping under any acceleration/ deceleration time and any impact load conditions.
5. By setting the parameters, can simply control to drive the asynchronous motor andꦉ the s♍ynchronous motor.
6. Simple servo function, servo positioning andꩲ spindle orientation
Application
Scheme 1 Torque control mode: As the required force of the diameter oꦡf the coil is different, inertia compensation algorithm automatically adjusts to k💛eep the linear velocity constant.
Scheme 2 Roll diameter calculation mode: According to the parameters such as coil diameter and material thickness, built-in automatic calculation module of reel diaဣmeter adjus𝓡ts to keep the linear velocity constant.
Scheme 3 PID feedback mode: Adjust the speed difference byౠ pulse PID feedback to keep the linear velocity constant.
This case adopts scheme 3, and the application site is a factory in Shenzhen Guangming New District. The debugging process and effect of the windiꩵng inverter are as follows:
4.1 Debugging process
(1) Wiring according to Figure 1;
(2) Setting the motor parameters according to ꩵthe motor nameplate;
(3) Disconnect the motor load, use the j💙og (JOG) function to determine the motor rotation direction, and change the wir🎉ing to rotate in the forward direction;
(4) Perform self-tuning of motor parameters;
(5) Setting the maximum o𝕴utput frequency and the upper limit frequency;
(6) Set🍸ting the command given channel and frequency given cha♏nnel;
(7) Setting the ꦰacceleration and deceleration time;
(8) Setting the terminal function;
4.2 The wiring of control signal
The wiring of control signal♛ is shown in Figure 1, where AI1 is frequency reference, DI1 is forward rotation, DI3 is reverse rotation, and DI6 is pulse PID feedback input.
4.3 Final parameter setting
4.4 Actual results
According to the field test, when the winding volume is about 600m, the change of the winding diameter is small, the PID pulse feedback amount is small, the winding isಌ smooth, and the coating is uniform. When the winding volume is from 600m to 1200m, t♎he change of the winding diameter is big. The speed is adjusted in time by the PID pulse feedback to keep the linear velocity constant, and then a good coating effect is obtained. The work has increased the efficiency by more than 20% in the original traditional way, reduced the dependence on the skill of the operator and improved the degree of automation. And also it has been highly praised by the users.
4.5 Debugging Precautions
1. It is necessary to obtain the motor parameters accurately, so it is necessary to input the motor꧅ nameplate value co𝔍rrectly and perform motor parameter self-tuning.
2. Need low-freq♏uency starting torque, just set F09.07 to 0 (automatic torque boost) to meet the requirements.
5 Summary
HD50 High-peformance Vector Control AC Drive has been successfully applied in the field of packaging machinery, its superior performance (low frequency torque, wide speed range, high steady-state accuracy, f🥀lexible operation, comprehension functional protection), a variety of control solutions and its high reliability have been fully verified and fully meets the coating machine process control requirements.